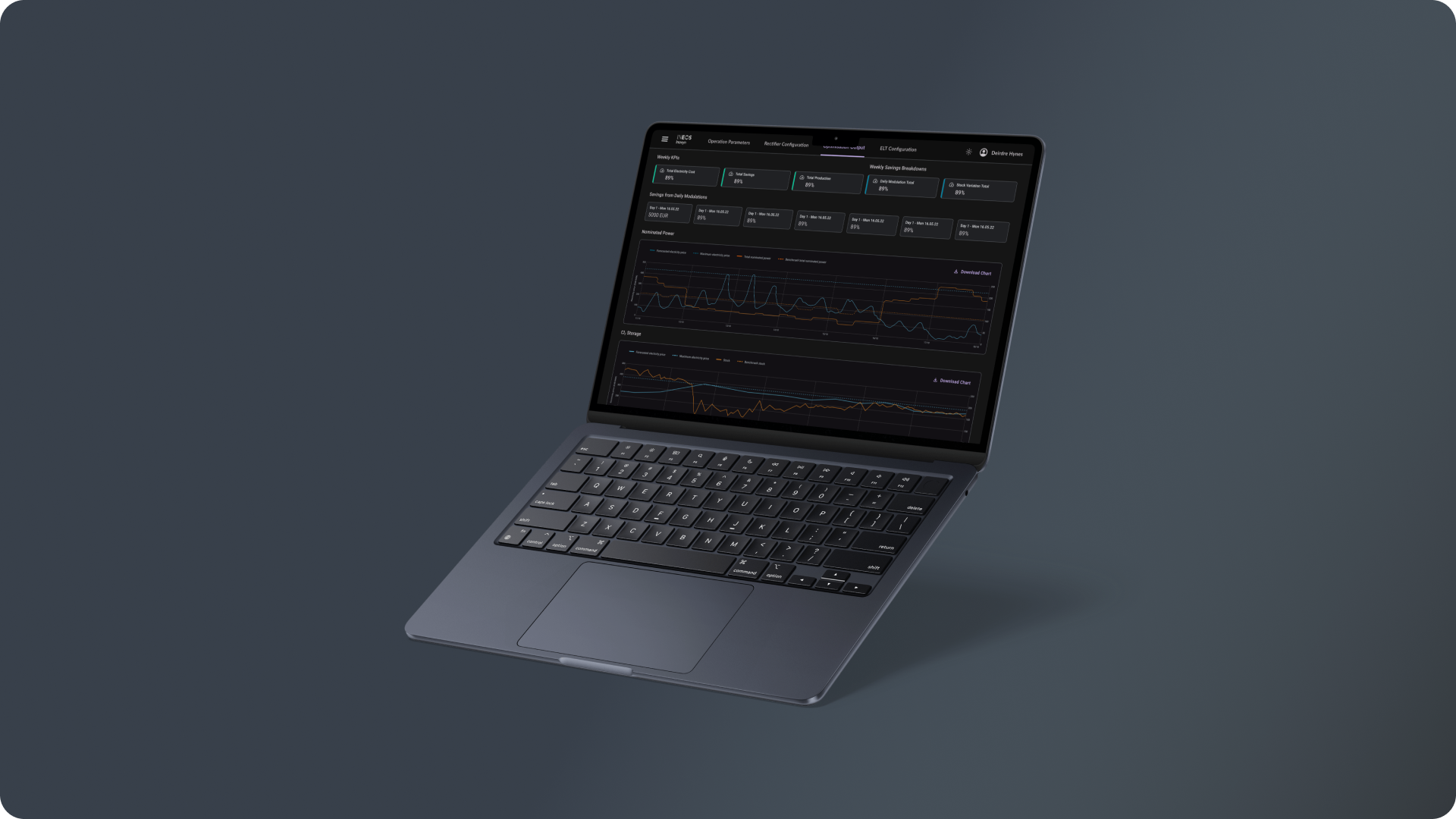
Client: INEOS Inovyn
Date: 2022 - Present
Industry: Petrochemical
Role: Lead Product Designer
Project Overview
INEOS, a global leader in petrochemicals with operations at 194 sites across 29 countries, is committed to sustainable innovation. With annual revenues of $65 billion, the company is focused on enhancing operational efficiency across its portfolio. In line with its goal to reduce scope 1 and 2 emissions by 33% by 2030 (compared to 2019 levels), INEOS partnered with Arundo Analytics to develop the Energy Optimizer—a tool designed to reduce energy costs and environmental impact in chlorine production at Inovyn, one of its key business units.
The Energy Optimizer uses advanced mathematical models and real-time data analysis to forecast electricity prices, enabling plants to schedule electrolysis—the most energy-intensive part of chlorine production—during periods of lower energy costs. This strategy not only reduces operational expenses but also minimizes reliance on carbon-intensive energy sources, supporting INEOS’s sustainability goals.
INEOS, a global leader in petrochemicals with operations at 194 sites across 29 countries, is committed to sustainable innovation. With annual revenues of $65 billion, the company is focused on enhancing operational efficiency across its portfolio. In line with its goal to reduce scope 1 and 2 emissions by 33% by 2030 (compared to 2019 levels), INEOS partnered with Arundo Analytics to develop the Energy Optimizer—a tool designed to reduce energy costs and environmental impact in chlorine production at Inovyn, one of its key business units.
The Energy Optimizer uses advanced mathematical models and real-time data analysis to forecast electricity prices, enabling plants to schedule electrolysis—the most energy-intensive part of chlorine production—during periods of lower energy costs. This strategy not only reduces operational expenses but also minimizes reliance on carbon-intensive energy sources, supporting INEOS’s sustainability goals.
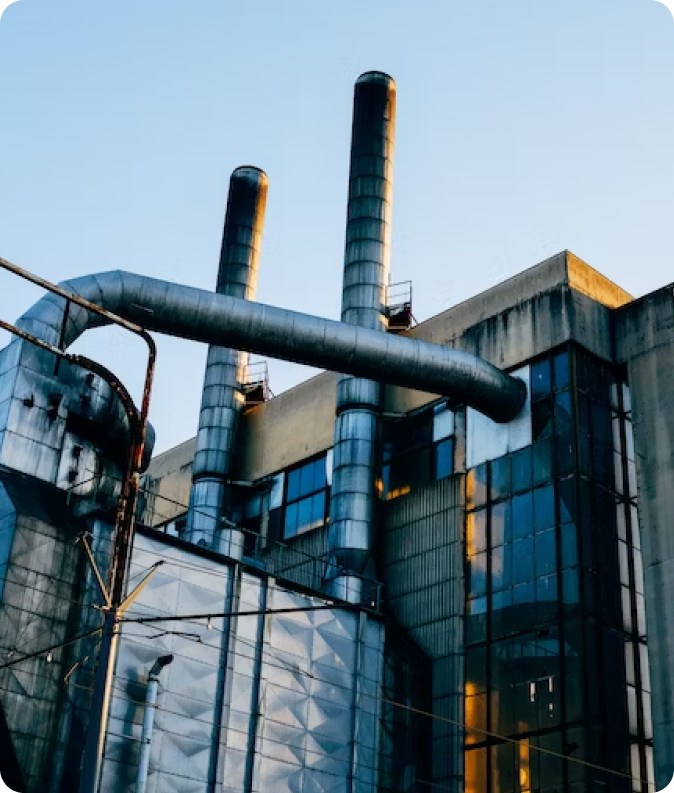
Design Challenges
As the lead product designer for the Energy Optimizer project, my responsibility was to transform complex data analytics into a simple interface that offered clear, actionable insights for technical users. The challenge was twofold: presenting highly technical data in an insightful way and ensuring the tool fit seamlessly into the existing workflows of plant operators.
To address these challenges, I collaborated closely with our data science team and conducted on-site research, including interviews and workflow observations. This research gave us a deep understanding of users' needs, pain points, and operational routines, and directly informed the design process
Key aspects of the research included:
· Identifying bottlenecks: We examined how operators interacted with existing systems to identify inefficiencies and common hurdles, especially where users felt overwhelmed by data.
· Understanding workflows: We observed day-to-day operations to find opportunities for improving efficiency and aligning the design with users’ natural workflows.
With this research in hand, I applied a few cardinal design principles to ensure that the Energy Optimizer would be practical and valuable for its users:
· Tailored User Experience: I mapped out the tasks users performed most frequently and designed the interface to support these actions. The UI was customized to reflect the routines and preferences of both novice and experienced operators.
· Simplified Data Presentation: Given the complexity of the data being processed, the design prioritized clarity—offering key insights at a glance while providing deeper layers of information only when necessary. This allowed users to make informed decisions quickly, without being overwhelmed by unnecessary detail.
Outcome: Enhancing Efficiency and Sustainability
The Energy Optimizer has been successfully implemented at multiple INEOS plants across Europe, driving both cost savings and energy efficiency. By optimizing when electrolysis takes place, the tool has reduced electricity expenses and minimized reliance on carbon-intensive energy sources. The solution has also helped INEOS make progress toward its sustainability goals, aligning with the company’s broader objective of reducing emissions by 2030.
As the lead product designer for the Energy Optimizer project, my responsibility was to transform complex data analytics into a simple interface that offered clear, actionable insights for technical users. The challenge was twofold: presenting highly technical data in an insightful way and ensuring the tool fit seamlessly into the existing workflows of plant operators.
To address these challenges, I collaborated closely with our data science team and conducted on-site research, including interviews and workflow observations. This research gave us a deep understanding of users' needs, pain points, and operational routines, and directly informed the design process
Key aspects of the research included:
· Identifying bottlenecks: We examined how operators interacted with existing systems to identify inefficiencies and common hurdles, especially where users felt overwhelmed by data.
· Understanding workflows: We observed day-to-day operations to find opportunities for improving efficiency and aligning the design with users’ natural workflows.
With this research in hand, I applied a few cardinal design principles to ensure that the Energy Optimizer would be practical and valuable for its users:
· Tailored User Experience: I mapped out the tasks users performed most frequently and designed the interface to support these actions. The UI was customized to reflect the routines and preferences of both novice and experienced operators.
· Simplified Data Presentation: Given the complexity of the data being processed, the design prioritized clarity—offering key insights at a glance while providing deeper layers of information only when necessary. This allowed users to make informed decisions quickly, without being overwhelmed by unnecessary detail.
Outcome: Enhancing Efficiency and Sustainability
The Energy Optimizer has been successfully implemented at multiple INEOS plants across Europe, driving both cost savings and energy efficiency. By optimizing when electrolysis takes place, the tool has reduced electricity expenses and minimized reliance on carbon-intensive energy sources. The solution has also helped INEOS make progress toward its sustainability goals, aligning with the company’s broader objective of reducing emissions by 2030.